A small medical supplies distributor in Belgium—one founder, no employees—decided to go all in on an ERP system. The goal? Automate orders, track inventory, and simplify accounting.
What happened instead? A total mess.
❌ Where It Went Wrong:
🔹 No Real Planning – The founder assumed the ERP would “just work.” No one mapped out how supplier pricing, customer orders, or inventory tracking should flow. The system didn’t match the business.
🔹 No Testing, No Training – Instead of running test orders, they launched it blind. The first real order? Wrong pricing, missing stock locations, total confusion.
🔹 Focusing on the Wrong Things – The founder spent more time tweaking report layouts and button positions than making sure orders processed correctly.
🔹 Trying to Use ERP Like Excel – They wanted strict processes and full flexibility. But an ERP isn’t a spreadsheet—you can’t make up rules on the fly.
The Result?
The system went live, but nothing worked. Orders got delayed, financials didn’t add up, and instead of making life easier, it just created more headaches.
Lesson learned? ERP isn’t magic. You need proper setup, testing, and a real plan. Otherwise, it’s just an expensive disaster.
💬 Have you ever seen an ERP project go completely wrong? What’s the worst mistake you’ve seen?
Drop your stories in the comments!
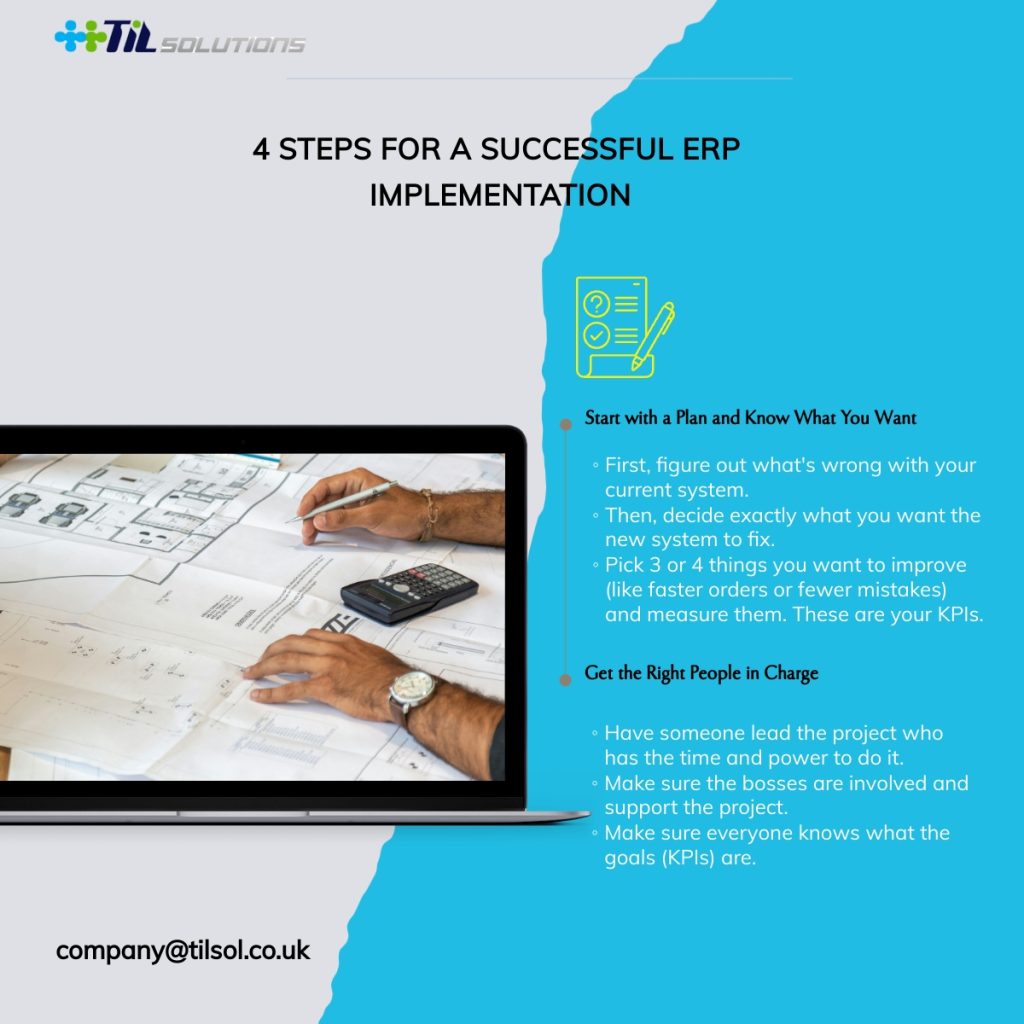
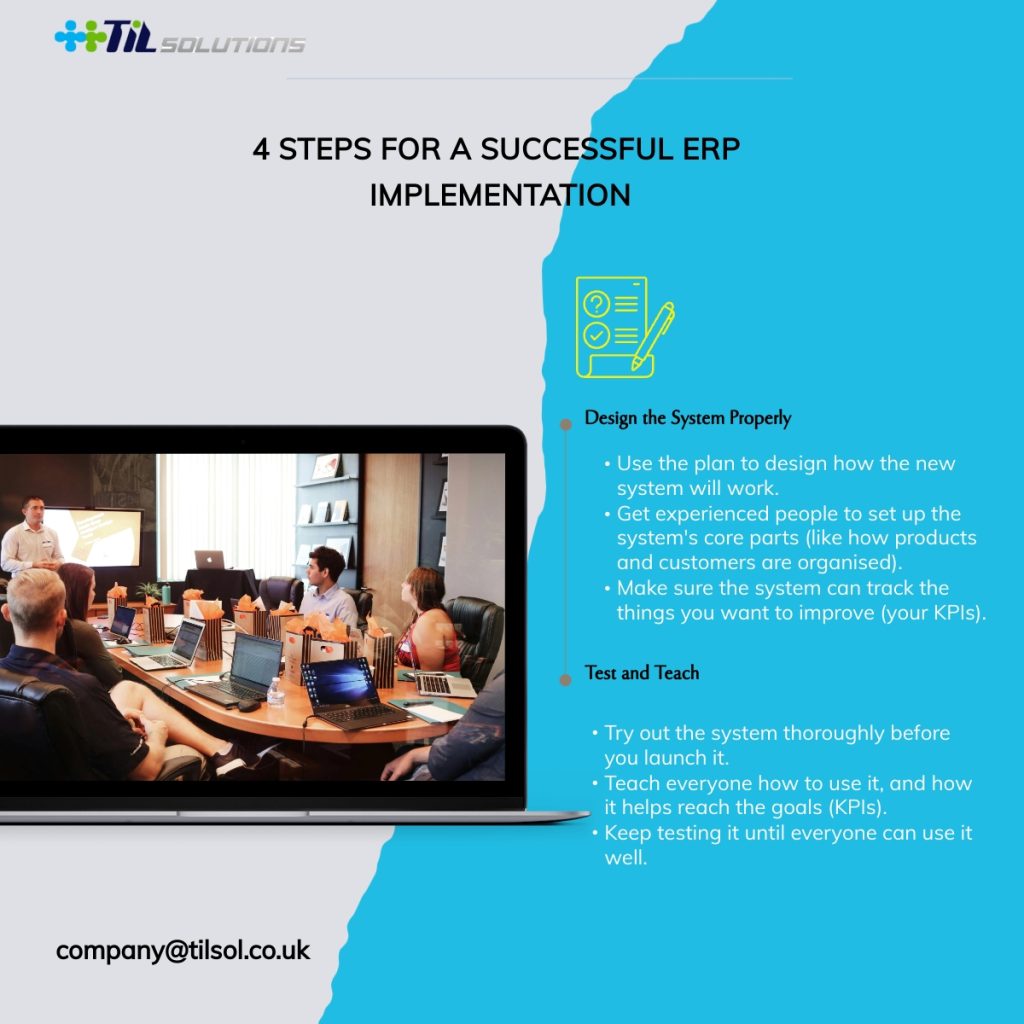